Roland welcomed DW Drums into its global family of brands in late 2022, just in time to contribute to DW’s wireless and acoustic-electronic drums, DWe. Built on handcrafted American-made Maple shells, DWe is powered by DW Soundworks™, a VST with the most authentic DW drum samples anywhere. Here is the continuing story of DW Drums from its earliest days as a teaching studio through its pivot to a revered manufacturer, right up to the latest innovations.
A Long Journey
DW’s breaking through into drum manufacturing didn’t happen overnight. Instead, it was a long and strenuous journey requiring people, resources, and yes, tons of innovation. As the company developed drums to build a market and sign artists, John Good took side jobs repairing drums and bearing edges for working session players in LA. He gained a reputation for fixing and tuning drums, which led to him being invited to studio sessions and eventually a job as a touring drum tech.
"As the company developed drums to build a market and sign artists, John Good took side jobs repairing drums and bearing edges for working session players in LA."
On the Road: Proof of Concept
On paper, this sounds like a disruption from developing instruments and hardware in the workshop. However, in practice, it served as a perfect environment for DW to observe the day-to-day hassles of a working drummer and develop creative gear to solve them. John’s season as a full-time drum tech started with tours for Earth, Wind & Fire and Men at Work in the early ’80s, then progressed onto bigger acts like Elton John and Madonna toward the end of the decade.
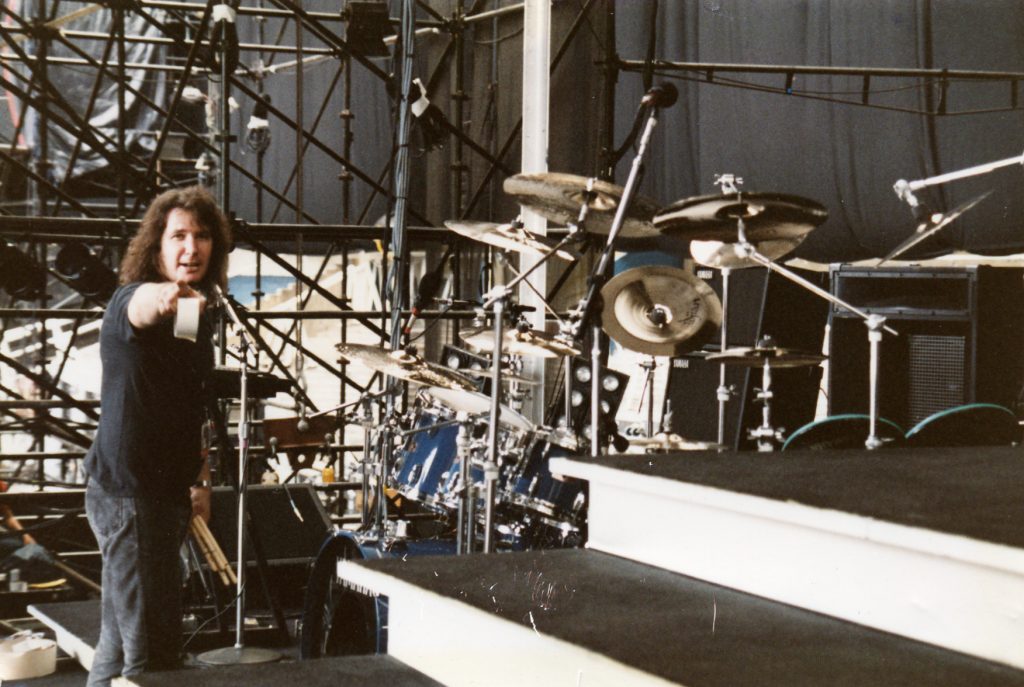
A Wide Open Endorsement
Back in LA, DW Drums was starting to build momentum thanks to some major players. Mötley Crüe’s Tommy Lee, an early adopter of DW pedals, had played a prototype kit at the workshop and fallen in love with their “wide open” sound. Now, at this point, DW had many drummers on the roster in legendary acts or working as popular educators. Still, Tommy’s endorsement put the company into popular culture for the first time. Shortly before Tommy took his DW Collector’s Series kit on the road to support Mötley Crüe’s Dr. Feelgood album, Don called John home to develop drums full-time.
"Mötley Crüe’s Tommy Lee, an early adopter of DW pedals, had played a prototype kit at the workshop and fallen in love with their 'wide open' sound."
Density and Tension: Building a Complete Instrument
Manufacturing is a proficiency-to-efficiency game, and drums were historically built with these lines of thinking. For example, mid-century factories would often build wood drum shells in batches, pair the different sizes together as a “set,” and send them to be finished and assembled. However, wood has varying degrees of density, and density and tension affect a drum’s sound. So, based on these factors, any two shells of any size could have a pitch that is the same or inverse. This can complicate tuning if multiple shells have no tonal separation between toms.
With early insight from Joe Montineri, John began tapping shells to ensure that the fundament notes of individual drums were matched in families with high-to-low intervals. To this day, after a set of DW Drums are timbre-matched, they travel through production as a family. Once that set of DW Collector’s Series shells is out of the paint shop, they’re tuned and labeled with the shell’s fundamental note, giving the drummer a baseline for tuning. This production method is still DW’s philosophy for making drums a more complete musical instrument.
"By layering individual plies cut to different grain directions—horizontal, diagonal, and vertical—DW could lower or raise the pitch of shells and increase resonance."
Enhancing Control
DW’s next game-changing drum shell technique was about enhancing control over drum timbre by changing grain orientations. The industry standard for wood shells was to layer plies with horizontal grain plies, but this method arranges the direction with the highest tension of the wood grain around the shell, increasing pitch. Conversely, the lowest tension of wood grain is vertical. By layering individual plies cut to different grain directions—horizontal, diagonal, and vertical—DW could lower or raise the pitch of shells and increase resonance.
The production team pioneered five new patented shell construction techniques in VLT (Vertical Low Timbre), HVLT (Horizontal Vertical Low Timbre), VLX (Vertical Low Diagonal), HVX (Horizontal Vertical Diagonal), and X-Shell (Diagonal). Each of these shells offers players a way to further customize their DW Drums for wider tonal range and nuance. In addition, this allowed DW’s team to ensure that every drum set has an intervallic relationship and performs as a complete musical instrument.
All About Nuance
The guiding light for DW Drums has always been innovation, which has resulted in over 50 patents since its foundation in 1972. Big, subjective drum breakthroughs like shell construction techniques to small, exacting changes like 30% more threads on tuning rods compound to create more options in your drum sound. And the desired result is to make the instrument more musical and to keep the drummer in the moment.